I. Installation Convenience: Standardized Interfaces Simplify Operation Processes
The flange adopts a standard interface design (such as international/industry standards like SAE, ISO), with precise matching between the interface size and the engine intake pipe. The bolt holes are pre-positioned, enabling “direct alignment installation” without additional modifications, reducing installation time by approximately 50% compared to non-standard interfaces. Due to the unified interface specifications, universal tools like wrenches and screwdrivers can complete the operation, avoiding reliance on special tools and significantly lowering the installation threshold.
II. Sealing Performance: Multiple Designs to Prevent Air Infiltration
The flange surface features extremely high machining precision, with a surface roughness ≤1.6μm and flatness error <0.1mm, minimizing gaps caused by surface irregularities from the source. It is paired with sealing materials such as oil-resistant rubber or metal wound gaskets, which maintain elasticity even in high-temperature environments to effectively fill flange gaps. When installing, tightening bolts uniformly according to the standard torque (e.g., 8-12N·m) avoids air leakage caused by insufficient local pressure. For example, a vehicle once experienced engine idle jitter due to poor sealing; after replacing the flange gasket, the mixture concentration deviation decreased from ±15% to ±3%, completely resolving the fault.
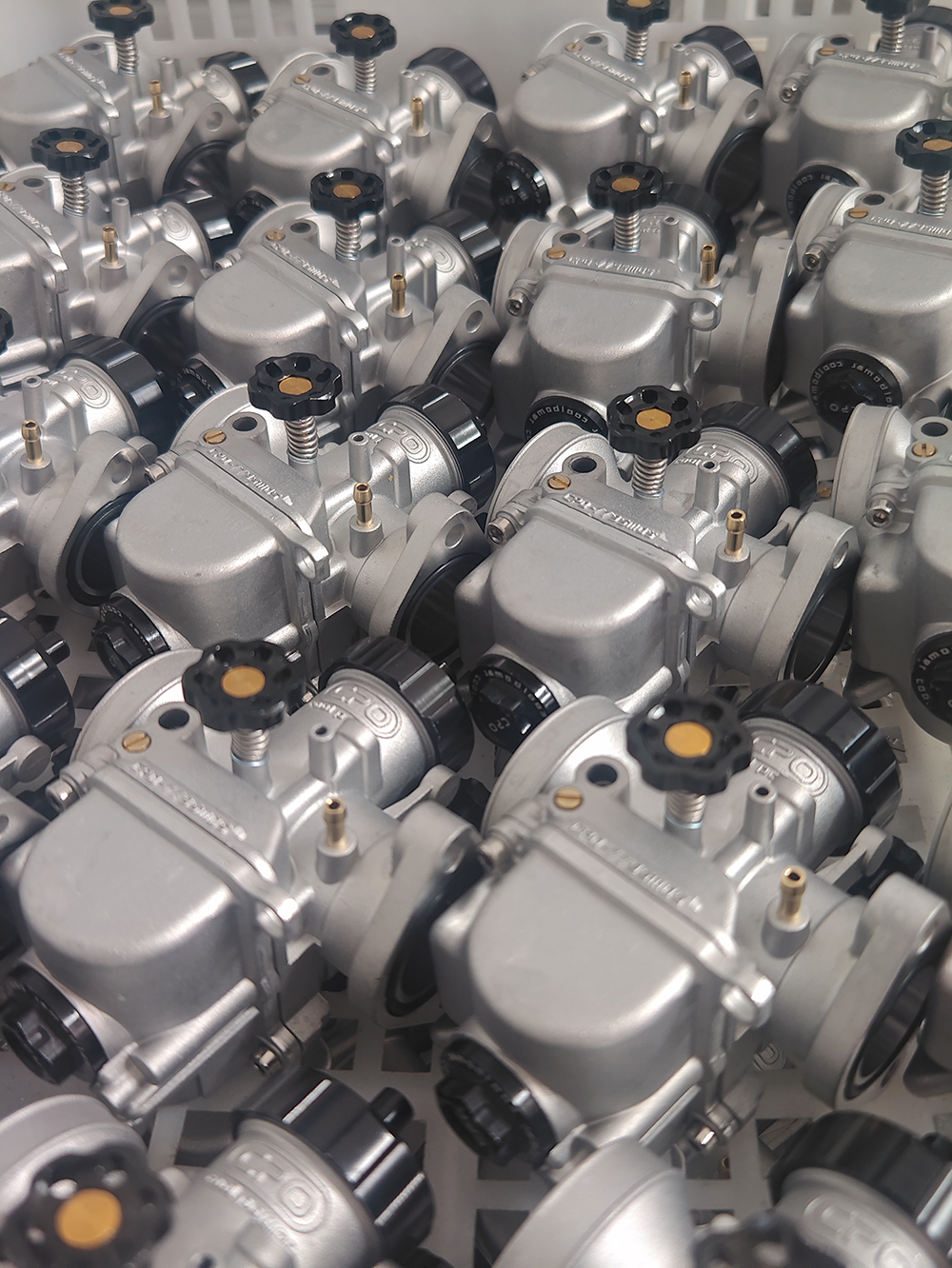
III. Adaptability: Modular Design for Cross-Platform Compatibility
Flange diameters cover various specifications from φ28mm (small motorcycles) to φ80mm (heavy trucks), while providing different interface types such as flat flanges, raised face flanges, and threaded flanges to adapt to different pipeline structures. This design makes it applicable not only to gasoline engines in older vehicles like the Santana and Jetta but also to diesel engines (e.g., some construction machinery) and non-road machinery such as generators, tractors, and marine power, significantly expanding the application scenarios of carburetors.
IV. Mixture Regulation: Structural Foundation for Precise Control
The flange is positioned close to the throttle, making adjustment devices like idle screws and main jets respond more directly. Its intake passage cross-sectional area adopts a standardized design to ensure flow calculation accuracy: during idle operation, precise air compensation of 0.8-1.2L/min is achieved through the flange bypass idle air passage; under full-load conditions, the main nozzle interacts with the flange intake volume to control the air-fuel ratio at 12.5-13.5:1, ensuring the engine receives an appropriate mixture under different working conditions.
V. Maintenance and Replacement: Low-Cost Quick Overhaul Solutions
The connection with standard 4-6 bolts makes disassembly more efficient, taking only 3-5 minutes to complete carburetor disassembly (10-15 minutes for non-flange interfaces). The single gasket cost is typically below $10, with a replacement cycle of 2-3 years, resulting in low maintenance costs. Additionally, overall carburetor disassembly avoids damage to engine pipelines, saving 30%-40% of maintenance labor costs compared to traditional connection methods.